Embedded Electronics and Sensors
Leveraging Ultrasonic Additive Manufacturing (UAM) for Embedded Electronics and Sensor Integration
Embedding sensors and electronics into parts allows engineers to collect in situ data, enables continuous health monitoring of components while in operation, and protects sensors and electronics from caustic and damaging environments. UAM allows the embedding of various types of electronics and sensors, including fiber optics, strain gauges, thermocouples, RF chips, and many more. The solid-state process does not damage the sensor; rather, the sensor is protected from environmental and other hazards. Engineers can design and build smart devices and other Internet-of-Things (IoT) products using UAM.
Ready to Get Started?
Let’s Make the Impossible, Possible.
Connect with our team to start get started today.
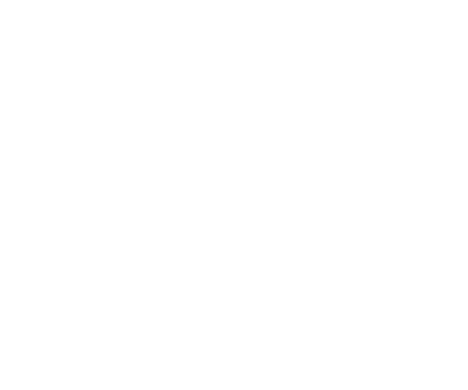
When performance matters most, we'll deliver.
ISO 9001:2015 Certified
Our scope of registration covers Ultrasonic Additive Manufacturing (UAM) Products, Equipment and R&D Services. Click here to download our certificate.
© Fabrisonic 2025 | 7719 Graphics Way Suite A, Lewis Center, OH 43035