News &
Updates
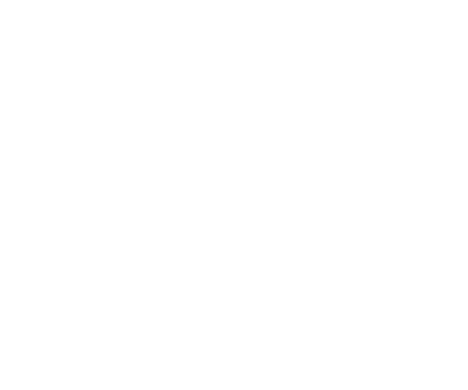
When performance matters most, we'll deliver.
ISO 9001:2015 Certified
Our scope of registration covers Ultrasonic Additive Manufacturing (UAM) Products, Equipment and R&D Services. Click here to download our certificate.
© Fabrisonic 2025 | 7719 Graphics Way Suite A, Lewis Center, OH 43035