WHO WE ARE
When performance matters most, we’ll deliver.
Fabrisonic® is an advanced manufacturing company that strives to inspire the world with new ways of making. Our patented hybrid manufacturing process allows customer to create new concepts impossible with traditional manufacturing.
In March, 2025, through United Performance Metals, Fabrisonic joined the O’Neal Industries Family of Companies, the nation’s largest family-owned network of metal service centers and component and tube manufacturing businesses.
Our dynamic team embraces these values:
- We dare to try.
- We collaborate, celebrating both shared success and failure.
- We believe details lead to customer success.
- We believe learning is a way of life.
- We enjoy the ride.
Meet The Team
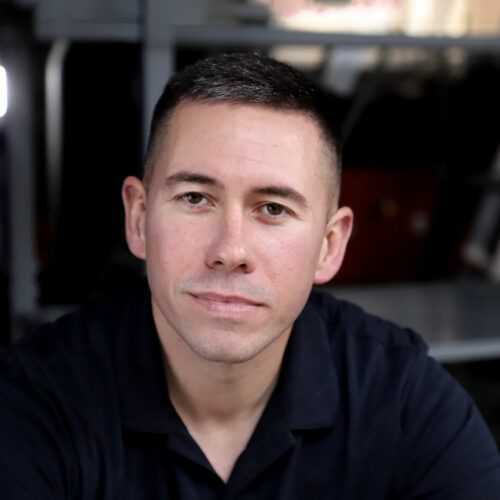

Luke is a Materials and Additive Engineer who graduated The Ohio State Univiersity in 2024 with a PhD in Welding Engineering. His research specialized in ultrasonic and resistance welding techniques for joining dissimilar materials. Luke is an expert in metallurgy and specifically, intermetallic compound formation and properties.
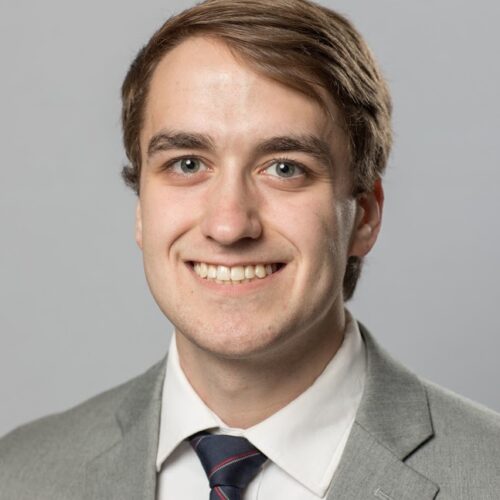
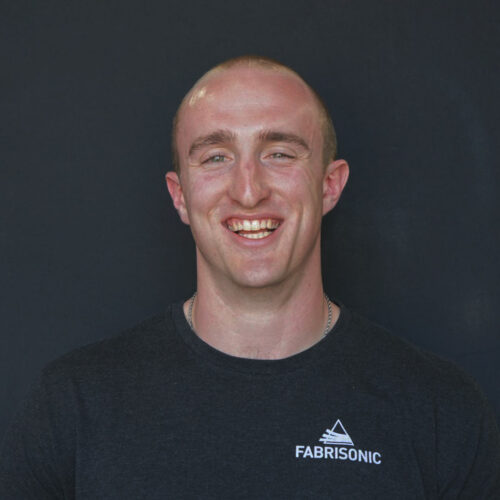
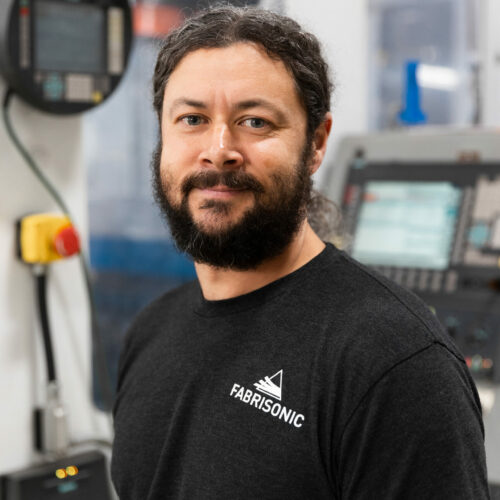
Brian utilizes more than 15 years of hands-on experience in fabrication and the manufacturing industry. He currently holds as A.A.S in electro-mechanical engineering. As the principal technician for Fabrisonic, he provides support for engineering staff, quality control and assists with production-based activities. His hobbies include, but are not limited to, playing music and being nice to rednecks.
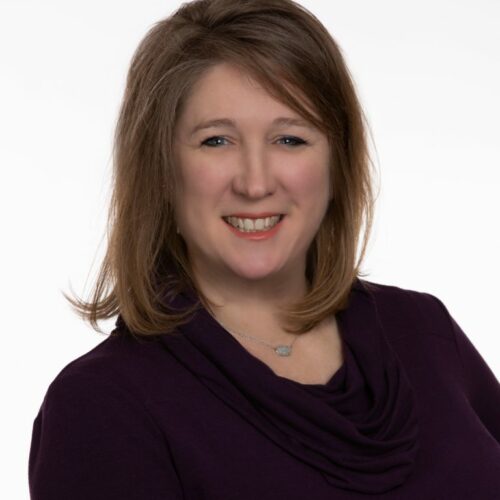
Maureen joined the company in 2018 as our inside sales representative. Maureen has been involved in sales, customer and marketing support across a number of industries over the past two decades. She provides the human touch to our highly technical world, helping to translate customer business requirements into engineering strategy. She has a bachelor’s degree in accounting from Simpson College.
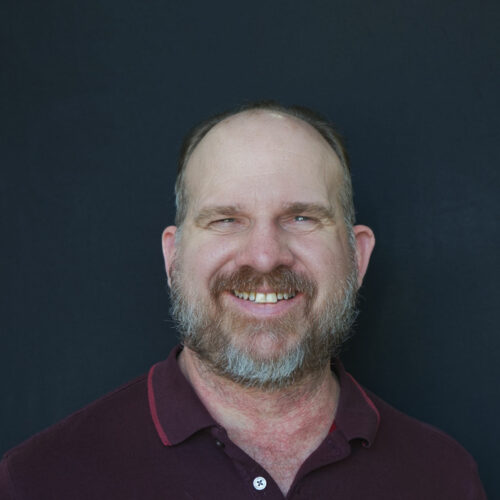
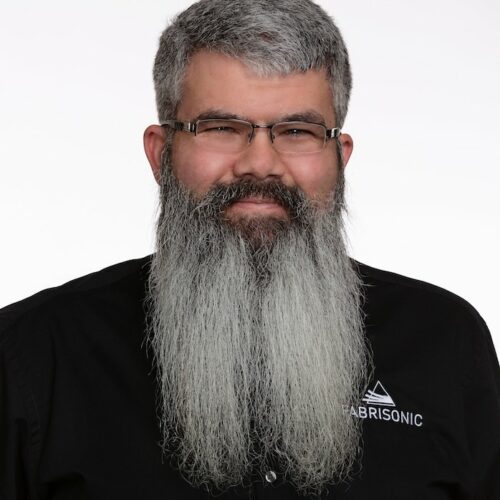
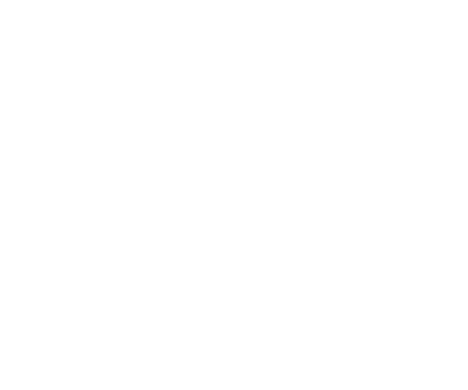
When performance matters most, we'll deliver.
ISO 9001:2015 Certified
Our scope of registration covers Ultrasonic Additive Manufacturing (UAM) Products, Equipment and R&D Services. Click here to download our certificate.
© Fabrisonic 2025 | 7719 Graphics Way Suite A, Lewis Center, OH 43035