3D Printing Heat Exchangers
Pushing the Boundaries with Additive Manufacturing in Heat Exchangers
Heat exchangers play a vital role in the performance of a wide band of industrial components in electronics, aerospace, power generation, and modern manufacturing. Increasingly, there is a need for high performance thermal management devices that can pull heat out of smaller and smaller areas at higher and higher rates. The push for increased efficiency of traditional thermal management devices has brought forth the need for designs only possible through 3D printing. Recently, Fabrisonic has made advances in the manufacturing of oscillating (or phase-change) heat pipes.
Ready to Get Started?
Let’s Make the Impossible, Possible.
Connect with our team to start get started today.
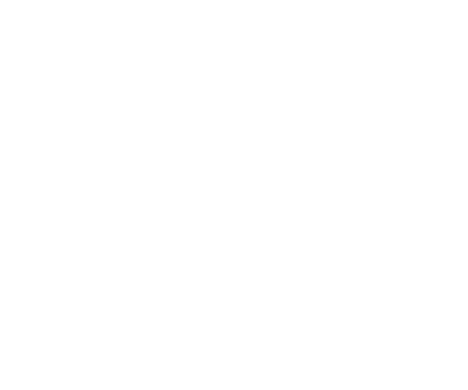
When performance matters most, we'll deliver.
ISO 9001:2015 Certified
Our scope of registration covers Ultrasonic Additive Manufacturing (UAM) Products, Equipment and R&D Services. Click here to download our certificate.
© Fabrisonic 2025 | 7719 Graphics Way Suite A, Lewis Center, OH 43035