OUR PATENTED TECHNOLOGY
Ultrasonic Additive Manufacturing
(UAM)
How Does It Work?
Ultrasonic additive manufacturing (UAM) works by using vibrations to weld successive layers of metal foil together, gradually building up a solid metal part. UAM systems integrate room temperature ultrasonic welding of foil with CNC machining to shape internal and external geometries. With a patented ultrasonic “print head” integrated into 3-axis mills, UAM seamlessly transitions between additive and subtractive manufacturing, enabling efficient production of customized parts.
WHAT UAM ENABLES
The Possibilities
Are Endless
Do you provide the feed material or can it be purchased from any raw metal provider? What are the requirements for it (geometrical form, dimensions and tolerances, weight, material)?
Foil can be found readily on the open market, and we can suggest vendors that work well for us. One issue that pops up during development is that many suppliers have a minimum order quantity of about 440 lbs. While this is fine for production applications, it can add costs to development or low volume manufacturing. If the material is one Fabrisonic stocks, we try to work with the customer to supply small quantities. With material that is costly, such as tantalum, we are able to get much smaller quantities in sheet form. In general, we look for foils with a mill finish rolled to a thickness between .05- .38mm (.002”-.015”). Foil tapes and sheet should be coiled on metal (preferred) or cardboard (usable) rings or cylinders. Our tape feeder can support a coil of minimum ID of 200mm (8”) and max ID of 500 mm (20”) with a max weight of ~ 20Kg. However, we can also accept customer materials as long as they can meet requirements which includes both tape and sheet.
I have read that the machine usually operates with 1” wide metal tape. Can it feed on tapes with different width? On sheets? If so, what are the limitations?
There are physics-based limitations to the width of the contact area of the welding surface which is approximately 1” wide. However, a wide variety of feedstocks can be used. Fabrisonic welding system is setup for a 1” wide tape. However, the guide rollers in the tape feeder can be easily swapped to allow for smaller width tapes.
Fabrisonic’s tape feed systems are not designed to feed sheet stock. However, sheet product can be presented to the machine manually, and the weld head can be rastered over the surface to weld an entire sheet. Care must be taken to prevent wrinkles in the sheet such as vacuuming the sheet in place. In the past, production machines have had an added pneumatic arm for picking up sheet from a hopper to the side of the machine and placing it in the proper location.
In general, the process is very forgiving of thickness variation but is sensitive to width variation. We have found that industry standard foil slitting machines hold a sufficient tolerance, but we have not quantified the tolerance on our own.
What materials work in the UAM process?
Fabrisonic has extensive experience with aerospace aluminums. Aluminums in the following series have all been welded successfully: 1xxx, 2xxx, 3xxx, 5xxx, 6xxx, 7xxx.
A myriad of dissimilar metal combinations have been successfully carried out including, Al/Cu, Al/Ti, Al/Fe, Al/Mo, Ni/Fe, Ni/Ti, Al/Ta, Al/Invar, Al/MMC’s. The following chart was developed for Ultrasonic Metal Welding (a precursor of UAM). While we have not tried all of these combinations, theoretically, they should be feasible.
The ultrasonic welding process is not suitable to join metals to non-metals.
However, non-metallics can be embedded into solid metal parts. Embedding reinforcing members such as boron and silicon carbide fibers or stainless steel meshes into metal matrices is simple with Ultrasonic Additive Manufacturing. Since the process can be interrupted and modified at any point, structural components can be augmented into any metal matrix to form superior, high performance composite structures. These advanced materials can be stiff and lightweight, the perfect combination for high stress, weight-critical environments.
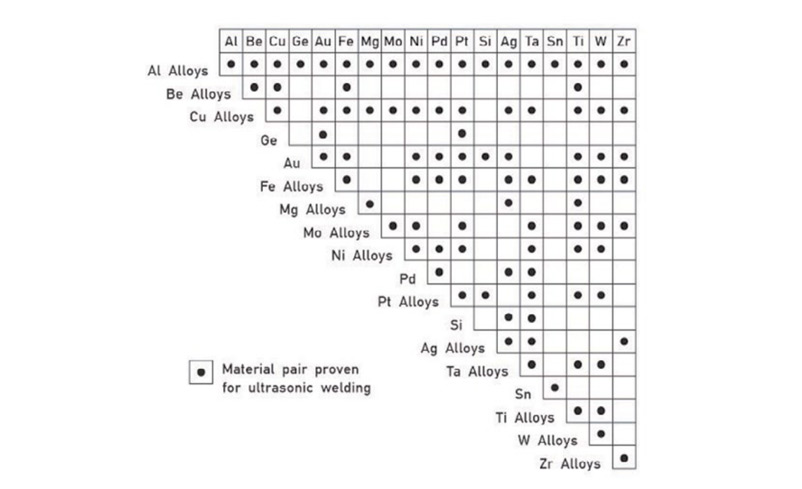
What temperature does the metal reach during the ultrasonic welding process? We understand that it’s a cold process, but what is the maximum temperature we should expect?
This is highly material dependent. In aluminums, we typically see a maximum temp of 140°C (284°F). Copper generally welds at a lower temperature. However, in titanium we find that the material needs to go above the Beta Transus (~880°C) to get good weld properties. We have also found that certain materials weld better when the baseplate is pre-heated. Typical pre-heat temperatures are 66-121°C (150-250°F).
How does the process affect embedded electronics? Are there limitations on sensitive equipment?
Obviously, care has to be taken to avoid creating an electrical short circuit. We typically wrap electronics with Kapton® tape (or similar) to isolate them electronically. The three main concerns with the process are the high down force (2000+ N), the vibration (40+ microns), at what temperature can the electronic/sensor/fiber handle. To avoid the high forces, we typically machine a pocket in a structure and drop the electronics in and weld over top. Depending on the depth of the pocket, the part may or may not see a load. With low amplitude (~20 micron), it is possible to embed glass without breakage. Fabrisonic typically runs small experiments with new electronic components to determine the max amplitude that can be used without damage to a particular embedded device.
How does the welded material behave after the process? Can coating be applied to the manufactured parts same as to standard parts?
For the most part, the welded material behaves the same as material machined out of normal plate product. The UAM process essentially cold rolls the material as it is welding which can affect the material properties. Coatings can still be applied per the normal processes. We have had success with anodizing, paints, and conversion coatings.
FAQs — Geometry
What is the surface finish? How close can you hold tolerances?
Fabrisonic’s production machines start out life as a commercial 3-Axis CNC mill. To the base mill, Fabrisonic adds it patented welding head for additive manufacturing. The print head is treated as another tool in the CNC tool change (see video below). The additive head is used to add material to produce a part that is near net shape. The mill can then be used to CNC machine final true shape. The hybrid system allows for a mirror-like final surface finish as well as tolerances of +/-.0005”. Tolerances are further improved in that the part has always been in one machine. There is no error generally associated with parts that have to be located in two or three machines during production.
The machine lays tapes side by side with a small overlap, how sensitive the process to tolerances? How does the machine ensure it?
This is an area where we are continually doing process improvement. If too much overlap is created, ridges form which can cause issues on subsequent layers. If not enough overlap is created, we get small linear defects between adjacent horizontal tapes. Our most current tape feeder design can hold standard tolerances on most geometries.
Are the layers waterproof? Gas proof?
We have made components that are waterproof and have passed helium leak tests down to 10-9 std cc/sec. However, we find that we must use a few layers of sheet directly above a channel (instead of tape) to ensure integrity due to varying edge-to-edge tape gaps on the micro scale. Additionally, special parameters with lighter force must be used for the first few layers above a channel to prevent tearing depending on the size of the gap.
What are the geometrical limitations of the process?
The first limitation is best described as a height-to-width ratio. Tall, skinny, structures, such as wall, looks like a simple beam. At a height-to-width ratio of about 0.7 the theoretical beam has a resonant frequency of 20 kHz. As we are inputting energy at 20 kHz, the structure is put into resonance, and fatigues if we get to a height to width ratio of 0.7-1.0. To avoid this limitation, we typically build tall structures wider than needed and machine afterward to get true net shape.
The second limitation is unsupported geometry. Our process uses several thousand newtons of force in order to create a bond. For structures such as overhangs, no normal force exists to push back and enable bonding. We have found, however, that it is possible to make shallow overhangs such as by using and undercut end mill. Additionally, we can build over enclosed cavities. In general, cavities of less than 15mm (.6”) are workable as the horn can weld on either side of the cavity. However, directly above the cavity there will be a region of poor bonding, even with additional layers. A rule of thumb is that the build will ‘heal’ after a height equal to the width of the channel. Also, welds over pockets or cavities will have slight deformation, or bow, on the “ceiling” due to Image courtesty of Harvey Tool the force applied during welding.
A good thing to keep in mind, the 1” wide horn should be engaged over 75% of the horn width with sold material. Otherwise, the horn will tip to the side and will create a flatness issues and leads to a poor bond. Larger voids can be encapsulated using workarounds. For instance, in larger structures one could machine a lip around a large void and placed a .75” plate on the lip. Subsequently, the weld can continue over the entire structure. The .75” plate would provide support for the build to continue.
Have you tried support material?
Support materials have always been important in the world of metal 3D printing to enable printing complex overhangs and intricate internal features. When it comes to Ultrasonic Additive Manufacturing (UAM), which is obviously the coolest of all the metal additive forms, many fillers have been tried. Some past examples are ice, rock candy, and even other metals. The key to a good support material for UAM is for it to be easy to add and remove from features without affecting the metal’s properties but still providing rock-solid support for welding.
Fabrisonic has been working with NASA on building out-of-this-world heat exchangers where support materials are sometimes necessary. Through these programs, we’ve come up with two support materials that could revolutionize the future of UAM printing heat exchangers, cold plates and even radio frequency devices. One invention is a highly stiffened water-soluble mix that can be easily added to features while printing and then simply flushed out of the part after printing is complete. Newly developed supports are helping push the boundary of what’s possible when printing with UAM.
What about overhung geometry?
If possible, we prefer to machine overhangs after welding using the CNC capability in our machines. By waiting until after welding we can avoid resonance and buckling modes. However, if the required part has an internal overhung geometry, we must address it during the build. We have found that there is a large market that supplies custom end mills that can cut below and around a given geometry.
Below you can find a chart of common undercut bits that we use:
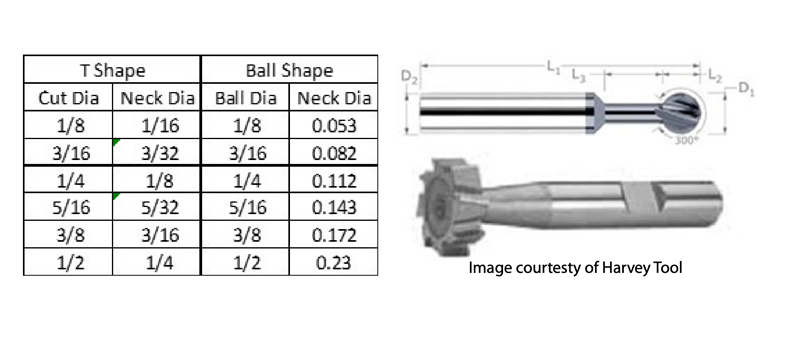
How does the welded material behave after the process? Can coating be applied to the manufactured parts same as to standard parts?
For the most part, the welded material behaves the same as material machined out of normal plate product. The UAM process essentially cold rolls the material as it is welding which can affect the material properties. Coatings can still be applied per the normal processes. We have had success with anodizing, paints, and conversion coatings.
FAQs — Process
How does an ultrasonic weld work? Is it a real weld?
Ultrasonic welding of metals has been around since the 1960s. The process uses ultrasonic vibrations to create a friction-like relative motion between two surfaces that are held together under pressure. This action, in turn, causes shearing and plastic deformation between asperities of the opposing surfaces, which disperses surface oxides and contaminants. As the asperities collapse, metal-to-metal contact is increased creating solid-state bonding between the parts through heat and pressure. The welds are truly metallurgically bonded without the need for heat or melting.
What are the parameters which control the welding process?
Key process variables for a given material include: welding speed, welding amplitude, welding force, and in some cases, preheat.
What is the build rate?
Many 3D printers measure material deposition in fractions of a cubic inch per hour. At these rates, parts are restricted to a small envelope that can be printed in a reasonable amount of time. Fabrisonic’s line of SonicLayer™ machines print from 15 to 30 cubic inches per hour. This allows for much larger build volumes.
The SonicLayer™ 4000 has a bed of 24 in x 36 in while the SonicLayer™ 7200 can accommodate parts 6 ft x 6 ft x 3 ft.
How do you program the machine? Do I need a special file format?
The SonicLayer™ series is controlled 100% through the use of industry standard G-code programming. The operator imports native CAD geometry into software that generates the tool paths for both welding and machining. The G-code is automatically generated and is then moved to the machine for execution.
What are the consumables for this machine?
There will be some maintenance of the horn. When it wears down, the welding surface will need to be retextured. When welding aluminum, a horn texture is good for several months of production. However, for harder materials like steel and titanium the horn could need retextured a few times a month.
The only other major consumables are standard milling consumables such as end mills, tool inserts, vacuum materials, oil/grease, and milling coolant.
Is the process of replacing milling tools an automated process or manual?
The SonicLayer™ 4000 and 7200 are commercial grade 3-Axis and sometimes 5-Axis CNC mills that we have integrated our welding system. Thus, it has an automatic 20 position tool changer built in, and all tools are called using traditional G-code commands.
Are there any special safety instructions for the ultrasonic process that we should be aware of? Safety distance from working machine? Special safety equipment?
The largest safety concern is noise level. We have measured sound of ~85 dB directly next to the machine. Hearing protection is recommended for those around the machine for long durations. In addition, typical safety standards are also recommended for operating this kind of machinery such as eye wear protection.
Ready to Get Started?
Let’s Make the Impossible, Possible.
Connect with our team to start get started today.
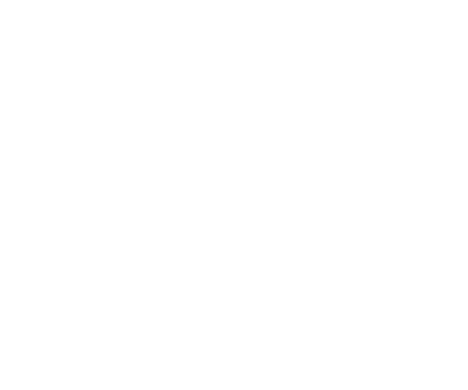
When performance matters most, we'll deliver.
ISO 9001:2015 Certified
Our scope of registration covers Ultrasonic Additive Manufacturing (UAM) Products, Equipment and R&D Services. Click here to download our certificate.
© Fabrisonic 2025 | 7719 Graphics Way Suite A, Lewis Center, OH 43035